Getting ISO 13485 Certified in College Station, Texas (TX)
Contact Us
Every company in College Station, Texas, worries about getting certifications and guaranteeing compliance in different ISOs to be able to offer the best. Those that need to get ISO 13485 are a great example of this. But, why are standards so important for companies and organizations? Do you actually have to meet them?
Since certain regulations and law requirements are established to guarantee companies offer the best but also, are the best in terms of how they operate, yes, ISOs are necessary. The requirements and guidelines established by each standard, either mandatory or voluntary, helps you to meet other legal regulations and, in the process, you’re able to improve your business. Overall, standards are indeed needed when it comes to improvements and requirements, but they are also great additions to boost your company’s growth.
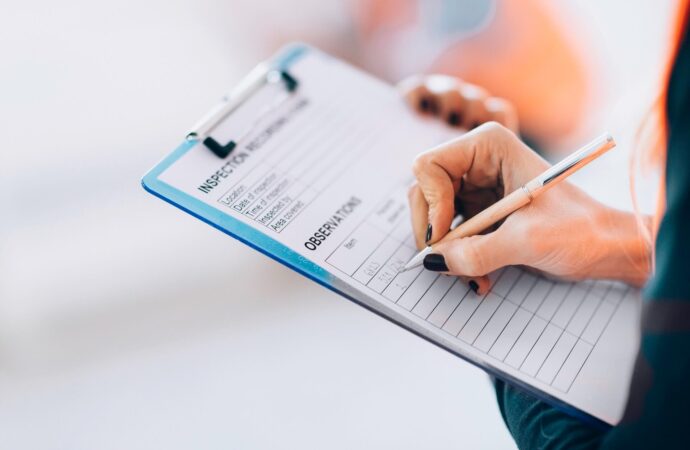
With that said, you will need to determine what standards you need and when to implement them to ensure they will not interrupt your operations. For companies in the aerospace industry, quality standards and those for the supply chain are mainly required. But for others like medical device manufacturers or companies, ISO 13485 is a better fit for their needs and also mandatory regulations.
ISO 13485 is a very specific standard that aims for the quality management system of every medical device manufacturer to ensure it offers top products and their performance won’t disappoint when used. Although quality is a very strict and necessary aspect in any company and manufacturer, medical devices have more to them than just the regular ones. From the very first process to the latest, it is necessary to meet all the operations accordingly to ensure there won’t be any issues with the device either when used right away or in the future.
However, implement standards that are for a specific company can be difficult for both new businesses or those manufacturers that have been in the industry for a while. The latest is usually a very weird case since it is a mandatory standard. But seems ISOs are being reviewed every few years, it isn’t impossible either considering several requirements and guidelines could be added.
The team at IQC The ISO Pros can help you to implement this standard for your medical device company to ensure you meet all requirements and regulations. Also, to guarantee you are able to deliver the top and high-quality devices for any customer and client. We work with three options: implementation, training, and consulting. You can either let our experts know which one you need or if you’re aiming for a mix of two or all three for your ISO.
Why you should implement ISO 13485
Leaving aside the fact of being a mandatory standard, let’s focus on why it is a benefit for your company. Overall, standards can be very expensive to implement due to all the processes and elements they involve. You have to change processes, operations, systems, and every aspect that guarantees you are meeting the requirements but also improving the company.
For medical devices and ISO 13485, everything is focused on the quality management system, but it entails more when you consider the benefits it brings to the entire production and manufacturing. With that said, the short answer to the question “is it worth implementing?”, would be ‘yes’ no matter what.
As a piece of advice, we suggest you look at standards as a way to improve your business, not as mandatory or just formal regulations you have to meet. This will make the process smoother and guarantee you are proceeding with the implementation in the right way. Also, that you are capable of looking at the changes and benefits.
Now, you should implement ISO 13485 mainly because of the improvements you will notice to your devices. The guidelines and requirements established are greater than any other standard for medical device manufacturers. Although ISO 9001 is also a quality management system normative, it is a generic one that offers guidelines for any company regardless of its size and type.
As a result, everything’s focused on different aspects and not on specific ones. Meanwhile, you’re able to boost your processes by addressing the right ones, guaranteeing the quality management system works properly and aimed at your needs. After all, implementing an ISO isn’t only about following every step established and all the documents, it is also about harmonizing it with your company’s needs.
In this case, you need to determine what you need for your QMS, how you can improve your devices, and if there’s a specific process that requires more attention. The great advantage of implementing this ISO also lies in demonstrating your competence and abilities. Clients and customers are more interested in hiring or acquiring products from those who meet every requirement and regulation but also, do their best to improve quality over the years.
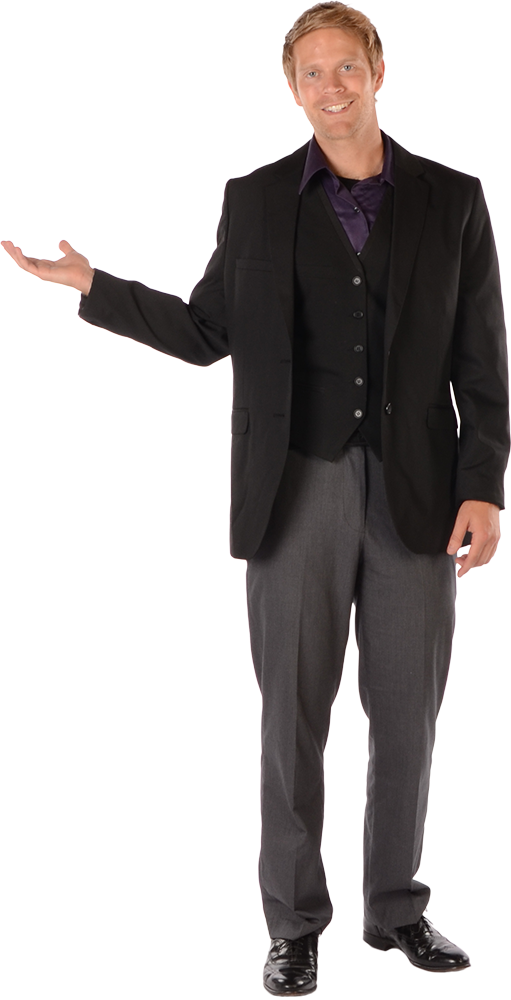
Who can implement ISO 13485?
The main condition is clear: you need to be a medical device manufacturer or a company related to it and mostly in the supply chain or involved in the process. But when it comes to general conditions and aspects that need to be considered, the truth is ISO 13485 can be implemented for everyone in the medical device business.
The size of the organization doesn’t matter as long as you adjust the requirements established and focus—as mentioned before—on your specific needs. With that said, size refers to the number of people working in your business. From 1 to maybe 100,000 or even 1 million people, you should implement it, and the sooner, the better.
Organizations that have been operating without ISO 13485 certification so far need to obtain it to ensure they are not limited nor closed. In certain states in the United States, it isn’t a mandatory standard despite being established by ISO and all the processes from other regulatory ones like ISO 9001. However, every medical device manufacturer in College Station, Texas, worries about demonstrating compliance and ensuring it is also able to offer the best and stay competitive.
Therefore, more than just being mandatory, make sure you are part of the group that implements it to bring more value to the company and have more relevance in the international market or, at least, in the local one.
What you need to know about ISO 13485:2016—current version
The last few changes and additions for the standard were made in 2016, but the last revision was only two years ago—2019—where the organization decided to leave everything just the same. Thus, whenever you are going to implement it, you need to go to 2016’s version and ensure you follow the guidelines in each part of the document.
With this clear, is there something you should consider when going for this certification? Absolutely.
It isn’t aimed at products.
Unlike what people believe, it does focus on the quality to ensure you are able to manufacture the best devices, but it isn’t aimed at the product itself. Since it works around the quality management system, the guidelines are to improve each process and operation in this area.
In this way, you should be able to obtain high-quality and optimal devices by the end of the day. It is a matter of addressing the processes and methods instead of the final result itself, which can be handled if you know you’re following the right procedure.
You cannot get a personal certification.
Although some standards are available for individuals, this isn’t the case. It is only available for companies and organizations that are part of the industry and need to guarantee compliance with the requirements.
Individuals can only become certifiers in order for them to provide it, but it isn’t a matter of getting ISO 13485 certified if you—maybe—produce personal devices but you’re not registered as a company.
Compliance doesn’t mean it is over.
The most common mistake is to think you don’t need to continue working in the quality management system. The main goal in ISO 13485 is to ensure the manufacturer is able to continuously improve this system and offer the best every single time.
Therefore, even if you fulfill compliance with the standard, you need to continue looking forward to improving and making things better. However, the standard will make this task much easier and simpler for your company while you’re able to meet other requirements and regulations that are usually mandatory.
Even when we mentioned the aspects to consider, you must understand that each version adds more value to another in different aspects—if it was changed and there’s another one. In the case of ISO 13485:2016, it has a better focus on risk, clarification of management responsibilities, training responsibilities, improvement to the facility, and many other aspects of the system and company overall. Therefore, you need to pay attention to what changes you will be dealing with when you are a company that is getting re-certified and there’s a new version. Or if you are implementing it for the first time so you can keep the focus of your needs harmonized with the ones of the ISO as well. In our experience, we would suggest you keep the focus on 3 to 5 different elements of the standard. However, you will find many more and not only a few. The idea is to implement every requirement as established, but if you can go for very specific ones, you should be able to achieve greater results. With this clear, let’s move onto more aspects to focus on: There are still many changes and additions in 2016’s version. Now, you might have noticed the aspects aren’t really related to the processes themselves but rather other elements in the company. This is important to point out because quality doesn’t involve procedures but also how you deal with your clients, make sure to deal with problems and complaints, control external elements that influence your medical devices, and more. As a result, you have a combination of what you need to do as the company itself and in your processes but also, what you need to consider when it comes to other external and internal aspects that influence it. As soon as you can. There’s no something as ‘the right time’ when it comes to ISOs. Instead, you have to aim for it once you decide to enter businesses. Since ISO 13485 is a mandatory standard for most medical device manufacturers in College Station, Texas, and any other city in the state, it is only natural to start in no time. At IQC The ISO Pros, we can help you by offering the best alone. Our team of experts will work with you to determine your needs, assess your current quality management system if it has been already established, and harmonize it with the implementation. If you are working from zero and establishing the system based on the requirements and guidelines right away, you will have it a bit easier. It is much better to implement the standard when you haven’t done much instead of readjusting or restructuring certain elements. However, with our help, you won’t have to worry too much about those aspects. Our professionals will work around your current situation and determine what’s the best way to proceed. Although the guidelines are pretty much established and you have clear steps, the truth is that you can approach the implementation and certification in different ways. And we will help you to identify the best one for you. Just contact us if you own a medical device company in College Station or throughout the state of Texas so our professionals can get there and start helping you with everything. What are the main focuses on the current ISO 13485 version?
When to start the implementation?
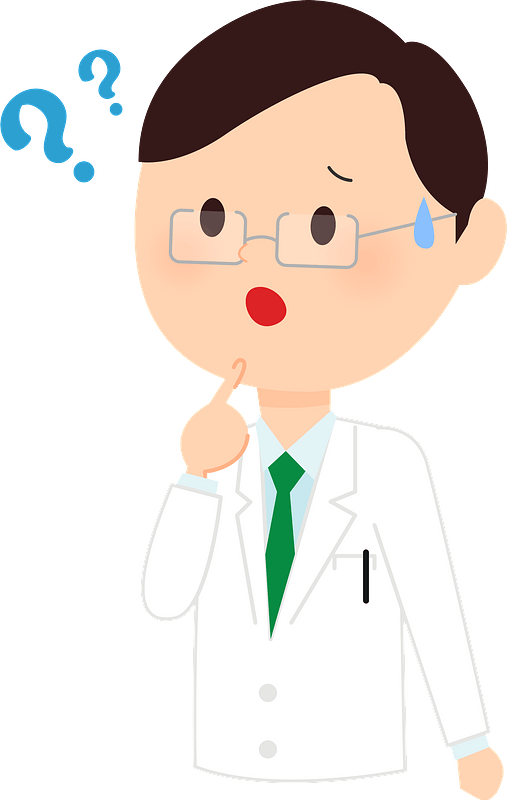